Fascination About Alcast Company
Table of ContentsAlcast Company Fundamentals ExplainedThings about Alcast CompanyAlcast Company - TruthsAn Unbiased View of Alcast CompanyRumored Buzz on Alcast CompanyThe Single Strategy To Use For Alcast Company
The refined difference depends on the chemical material. Chemical Comparison of Cast Light weight aluminum Alloys Silicon promotes castability by lowering the alloy's melting temperature level and enhancing fluidity throughout casting. It plays a critical function in allowing detailed molds to be loaded precisely. Additionally, silicon adds to the alloy's strength and put on resistance, making it important in applications where longevity is essential, such as vehicle parts and engine elements.It additionally boosts the machinability of the alloy, making it much easier to process into ended up items. In this way, iron contributes to the total workability of aluminum alloys.
Manganese adds to the stamina of aluminum alloys and boosts workability. Magnesium is a light-weight component that provides strength and influence resistance to aluminum alloys.
Alcast Company for Beginners
It enables the production of light-weight elements with outstanding mechanical residential or commercial properties. Zinc boosts the castability of aluminum alloys and aids control the solidification process during spreading. It boosts the alloy's toughness and solidity. It is frequently found in applications where complex shapes and fine information are essential, such as ornamental spreadings and certain vehicle parts.
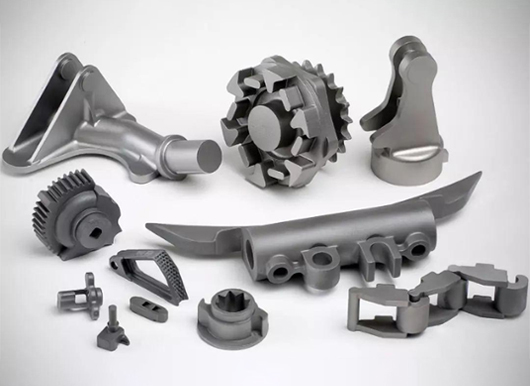
The primary thermal conductivity, tensile stamina, yield strength, and elongation differ. Select suitable raw materials according to the efficiency of the target product produced. Among the above alloys, A356 has the greatest thermal conductivity, and A380 and ADC12 have the cheapest. The tensile limitation is the opposite. A360 has the best return toughness and the highest possible elongation price.
All about Alcast Company
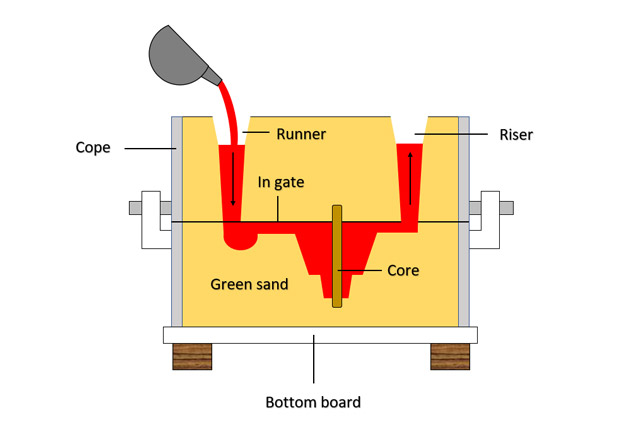
In precision spreading, 6063 is appropriate for applications where detailed geometries and high-quality surface coatings are vital. Instances include telecommunication units, where the alloy's exceptional formability allows for streamlined and visually pleasing styles while maintaining architectural stability. In the Lighting Solutions market, precision-cast 6063 parts produce sophisticated and efficient lights fixtures that need detailed shapes and great thermal efficiency.
The A360 exhibits premium elongation, making it optimal for facility and thin-walled parts. In precision spreading applications, A360 is well-suited for industries such as Customer Electronic Devices, Telecommunication, and Power Tools.
The Alcast Company Statements
Its special buildings make A360 a valuable selection for precision casting in these industries, boosting product longevity and quality. Aluminum alloy 380, or A380, is a widely utilized spreading alloy with numerous unique characteristics. It offers outstanding castability, making it an excellent choice for precision spreading. A380 shows good fluidity when molten, ensuring elaborate and detailed molds are accurately recreated.
In precision spreading, aluminum 413 radiates in the Consumer Electronic Devices and Power Tools industries. It's commonly used to craft elaborate components like mobile phone real estates, cam bodies, and power device casings. Its accuracy is amazing, with limited tolerances as much as 0.01 mm, ensuring flawless product setting up. This alloy's exceptional rust resistance makes it a superb option for outdoor applications, ensuring long-lasting, resilient products in the discussed industries.
All about Alcast Company
The light weight aluminum alloy you choose will substantially impact both the spreading procedure and the properties of the last product. Because of this, you have to make your choice thoroughly and take an educated approach.
Figuring out the most appropriate light weight aluminum alloy for your application will certainly indicate weighing a large range of qualities. The first category addresses alloy features that impact the manufacturing process.
About Alcast Company
The alloy you choose for die casting directly affects several facets of the spreading procedure, like exactly how simple the alloy is to function with and if it is vulnerable to Click This Link casting problems. Warm splitting, additionally known as solidification cracking, is a typical die casting issue for light weight aluminum alloys that can cause internal or surface-level splits or splits.
Particular aluminum alloys are more prone to hot breaking than others, and your selection needs to consider this. An additional usual problem found in the die casting of light weight aluminum is pass away soldering, which is when the cast adheres to the die walls and makes ejection tough. It can harm both the cast and the die, so you should look for alloys with high anti-soldering residential properties.
Rust resistance, which is currently a notable characteristic of light weight aluminum, can vary significantly from alloy to alloy and is a vital characteristic to take into consideration depending on the environmental problems your product will certainly be exposed to (Casting Foundry). Wear resistance is an additional home frequently sought in light weight aluminum products and can set apart some alloys